A pump test refers to various examinations that ensure pumps function optimally. Some pump tests are carried out after pump assembly. Some are performed after the pumping system is mounted at the site, and others are performed during pump commissioning. The aim of all pump tests is to ensure functionality of the equipment, reducing downtime and need for maintenance. In addition, they ensure the pump runs under the best possible proven protocols, limits and specification ranges as set by standard bodies including the American National Standards Institute (ANSI), Hydraulic institute (HI) and the American Petroleum Institute (API), depending on the pump type and configuration.
This pump test usually occurs at the point of assembly from the manufacturer’s factory to the loading station and ultimately the client, who receives the equipment for installation and operation. Visual inspection involves checking the pump for any visible or outward defects, including the pump casing, piping and components such as mechanical seals/gland packing, constant oil leveler, breather and shaft-free rotation in accordance and compliance with Manufacturers Standardization Society (MSS) SP-55. Spline Hydraulic Pump Couplings
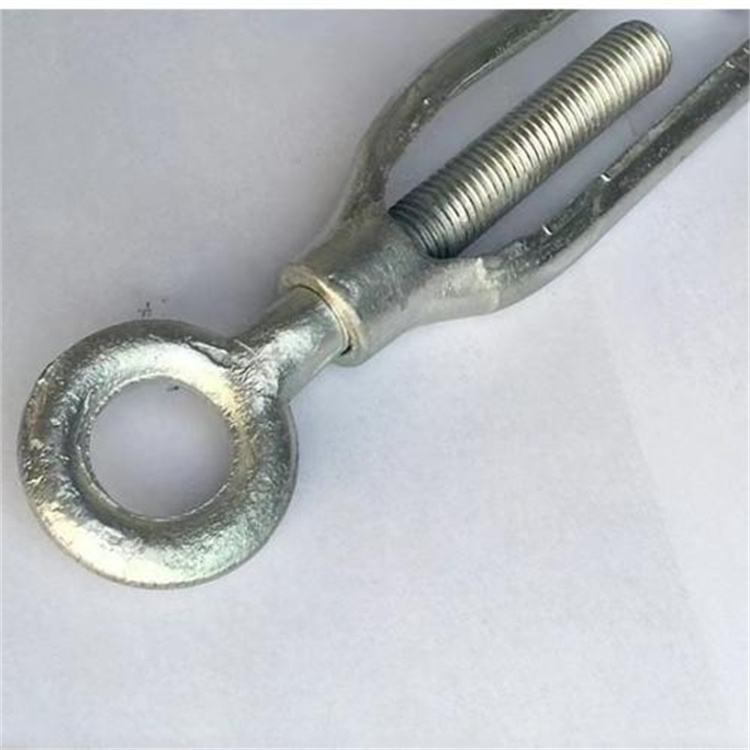
Pump runout is a pump test that is carried out to confirm the eccentricity of the pump shaft or the shaft and the coupling. The essence of pump shaft runout is to allow for proper pump linearity. This reduces rotor strain, coupling damage and excessive vibration which reduces pump efficiency and leads to damage. This increases cost of pump ownership and downtime, which may accrue from plant unavailability cost. Most manufacturers allow a pump runout limit of 0.002 inches for pumps running at a speed of 1,800 rotations per minute (rpm) or less and a limit of 0.001 inches for pumps running no less than 3,600 rpm. The shaft runout test verifies the condition of the shaft.
Dimensional checks of a pump are usually issued by pump manufacturers to a client. This is confirmed by the quality assurance unit of the manufacturer; however, field experience has shown there could be errors in a pump manufacturer’s dimensional checks. In one instance, during the commissioning of a pump, a rotor could not rotate within the pump casing. The client checked for the rotor float to confirm the impellers were not stuck within the casing. Thereafter, pump bearings (journal and thrust) were inspected and were found to be in good condition. Hence, the dimensional checks of the rotor were verified, and the results confirmed the dimensions deviated slightly from the manufacturer’s dimensional report. The pump was reassembled and shipped back to the manufacturer for corrections. Implications of dimensional errors can be limited by performing free rotation of the pump rotor within the machine upon receipt of the equipment. Additionally, the client, upon receiving equipment, should confirm receipt of the dimensional test report with signatories of the manufacturers.
Hydrostatic testing of a pump casing is performed by the pump manufacturer; however, the client must check the pump hydrostatic test report. This report is usually part of the test report provided by the pump manufacturer. Pump hydrostatic tests are performed in accordance with API, HI and ANSI regulations. The hydrostatic test is carried out on a pump using a multiplier of 1.5. This test ensures a pump casing can withstand the maximum discharge pressure of the pump, giving allowance or margin of safety.
According to API 610, hydrostatic tests must be performed, and leakage must be checked for 30 minutes. ANSI standard and practice for process industry states leakage checks must be performed under 10 minutes, while HI states leakage for equipment under 100 horsepower (hp) must be tested for 3 minutes and equipment greater than 100 hp should be tested for 10 minutes.
Dynamic balancing is performed on pump rotors to confirm there is no unbalance on the rotor. Unbalance on rotors occurs due to irregular mass distribution across the rotor. Hence, dynamic balancing is used to detect mass distribution across the rotor and detect the position of imbalance. Manufacturing anomalies are the primary cause of unbalance in pumps. Anomalies such as casting and rotor machining may be corrected by balancing impellers in a single plane. Impellers are recommended to be balanced to G2.5, according to the international standard (ISO) defined standard 21940-11. Procedures for high-energy pump rotor balancing are given by the ANSI/HI.
API, 610, 7th Edition, Centrifugal pumps for general refinery services, 1989.
Hydraulic Institute Test Standards for Centrifugal Pumps- 1.6, 1988.
V.P. Patel, M.W. Kellogg and J. Bro., Centrifugal pumps inspection and testing, Proceedings of the Twelfth International Pump Users Symposium, 143-150, 1995.
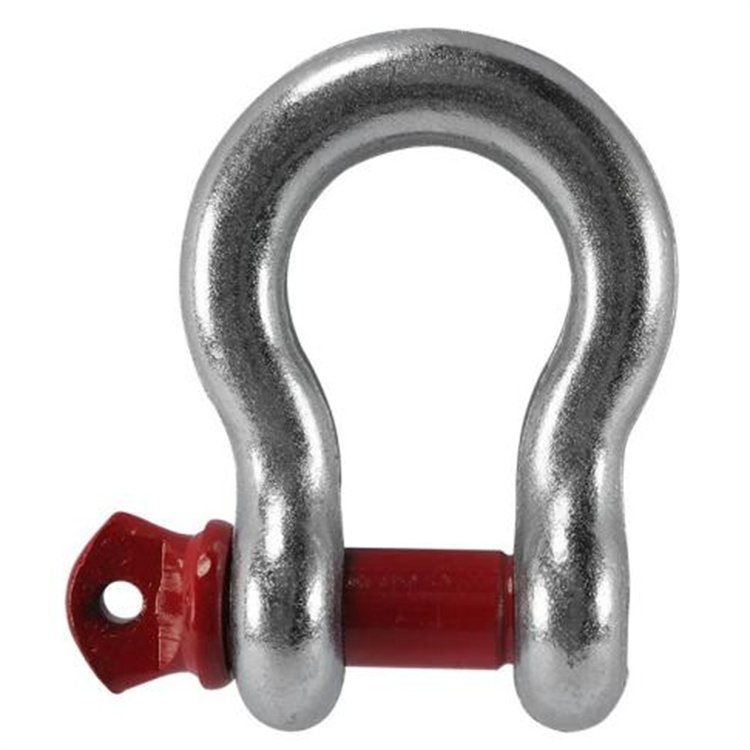
Types Of Retaining Pins Akinbowale T. Akinshilo is principal mechanical engineer for Dangote Fertilisers Ltd., in Lekki Free Zone, Lagos, Nigeria. He may be reached at akinbowale.akinshilo@dangote.com or ta.akinshilo@gmail.com.