At Fakuma 2023, Sumitomo (SHI) Demag’s LSR injection molding machines showcased advances from itself and partners Reinhardt-Technik, Rico and Sepro. #industry4-0
At its own and at a partner booth during Fakuma 2023, Sumitomo (SHI) Demag showcased advances in servo-driven dispensing, cold-runner tooling and customized automation for liquid silicone rubber (LSR) injection molding in two demo cells. On its main stand, the company highlighted multicavity LSR processing on its all-electric IntElect 180/570-250 injection molding machine, with another LSR cell at partner Reinhardt-Technik’s booth. Clean Room For Simiconductor
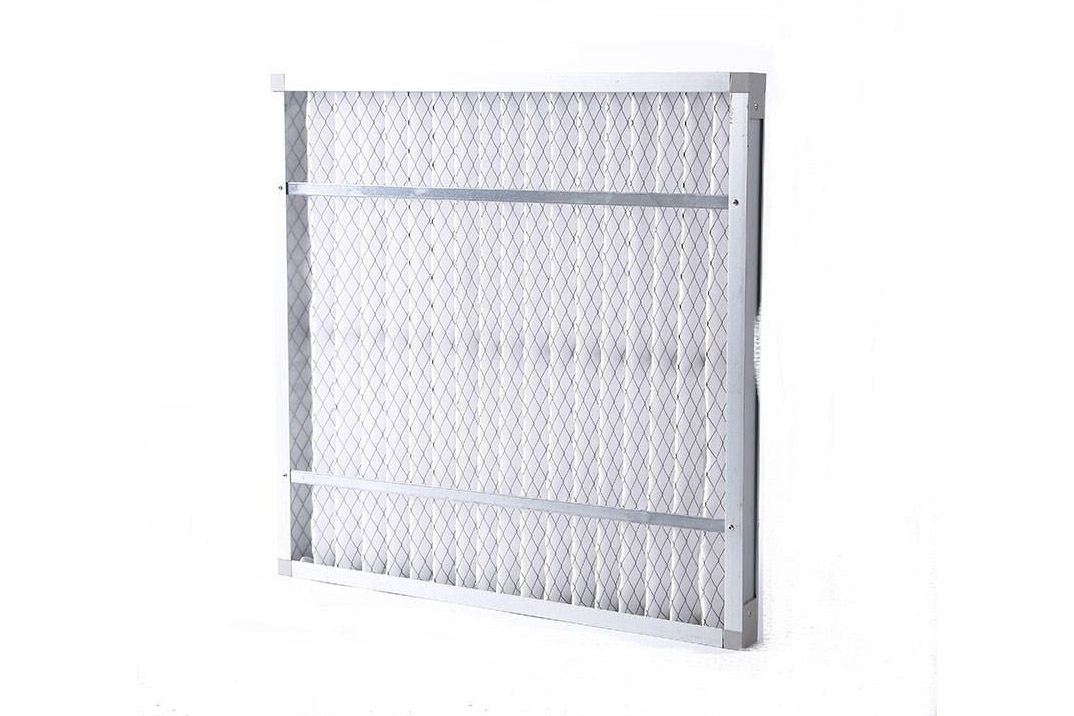
In its booth, Sumitomo (SHI) Demag’s IntElect machine was outfitted with a twin dosing system, automation, vacuum and venting peripherals. In a cycle time of 15 seconds, this IntElect LSR package molded 256 individual 0.06g single-wire seals from a 15g shot with extremely low energy consumption. LSR tooling manufacturer Rico supplied the 256-cavity mold, with Elastosil LR 3844/50 material from Wacker Chemie. That material was dispensed via ReinhardtTechnik’s compact Industry 4.0-ready LSR eTwin Connect dosing system. In addition to precision mixing of two LSR precursors, ReinhardtTechnik says its system ensures that 99.75% of the LSR material is processed.
OPC UA interfaces enable communication between the IntElect machine control and the eTwin Connect dosing system, with the 15.6-in. HMI capturing all processing documentation, including material pressure, as well as coloring and additive settings.
ReinhardtTechnik says its eTwin servo-driven piston pumps can save processors up to 80% energy consumption compared to pneumatically driven versions. The metering system’s integrated cooling and pulsation-free flow optimize filling and prevent the LSR from premature curing. The unit also performs automatic venting, purging air from the material before it is fed into the machine and tool. Modular by design, the LSR eTwin Connect enables quick program configuration and software updates. To support quick drum changes and for ease of maintenance, the system also features a roll-in device and automatic drum locks.
Rico describes its 256-cavity tool as proprietary, utilizing a direct injection system and double-nozzle technology. The 256 parts were molded in a 15-second cycle on a 130-ton IntElect. Despite the high cavitation, the compact mold measures 17.5 × 24 × 14 inches. The self-balancing cold runner and double-nozzle system were developed in-house with the cold runner nozzles applying a 1:2 ratio with optimal heat balance. Rico says the dual demolding system enables bulk production with individual, separated part removal. The demolding is automated via a specially adapted gripper plate that contributes to the 15-second cycle.
The cell also featured a customized Sepro SDR 22X robot which extracts all 256 parts versus letting them fall. Still manipulating all 256 parts, the robot delivers them to individual receptacles that feed smaller packing boxes. This enables molders to track which cavity the individual parts were molded in with the OPC interface connecting to the IntElect processing data for full traceability. This automation also gives molders the option to deposit a seal at defined intervals into a quality control drawer for inspection.
At Reinhardt-Technik’s booth, thin-wall surgical, dental protection covers were molded in a 25-second cycle from LSR on an IntElect 75/420-65 using a 4-cavity tool from EMDE MoldTec. Each part weighs just 0.425g and is generated from a 1.7g shot. Here too a Reinhardt-Technik eTwin Connect metering system delivers material to the needle-gate-nozzle tool with metering data and the IntElect’s processing data shared via OPC-UA for a traceable, stable production process. A Sumitomo (SHI) Demag SAM-C5 robot performs demolding, utilizing a specialized end-of-arm-tool to extract and place the dental covers into containers.
At Fakuma 2023, this Rico LSR tool ran on a Sumitomo (SHI) Demag IntElect injection molding machine. Photo Credit: Sumitomo (SHI) Demag
New technology from Glycon takes real-time measurements of screw and barrel wear and provides data to guide processors as to when the time may be right to swap out these components.
These four short videos provide a snapshot of what’s going on in plastics resin drying technology. Yes, there’s Industry 4.0, but also lots more to bring higher quality and efficiency to your injection molding and extrusion processes.
Learn why—and how—innovative molders have begun to develop “smart factories,” using advanced equipment, IT, and communication technology to enable greater connectivity and productivity.
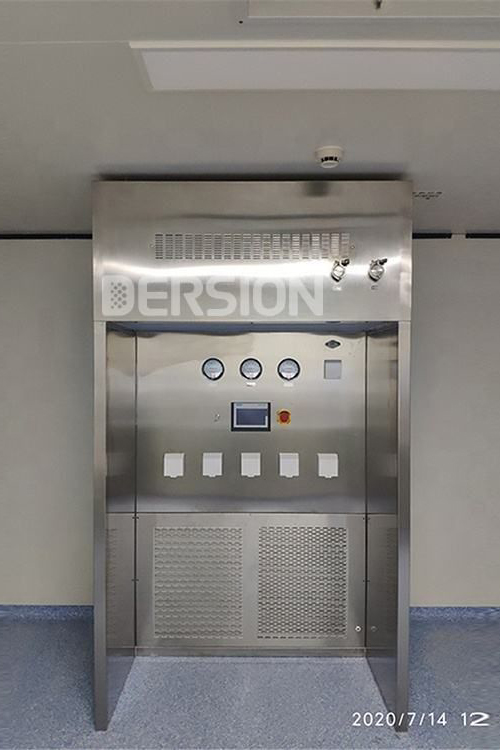
Pharmaceutical Clean Booth Sandwich Panels Clean Room © 2023 Gardner Business Media, Inc. Privacy Policy [Log On]